1.Aluminum slab quality control
All casting machines adopt the latest generation of semi-continuous low-liquid vertical shaft casting technology from WAGSTAFF. It is equipped with ABB's electromagnetic stirring, online hydrogen measurement and online slag measurement system. The on-line treatment of aluminum melt adopts the French NOVELIS on-line degassing system, deep bed filtration system, Japanese Mitsui Metal's plate filter and tubular filter, the degassing efficiency reaches 0.12ml/100g-AL, and the filtration efficiency reaches 98% or more (impurities below 10μm ).
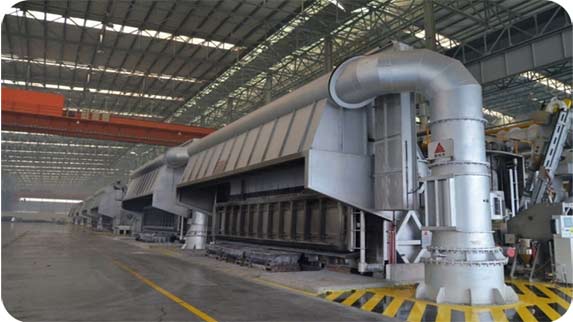
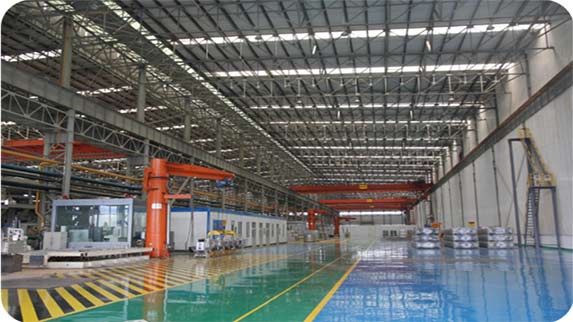
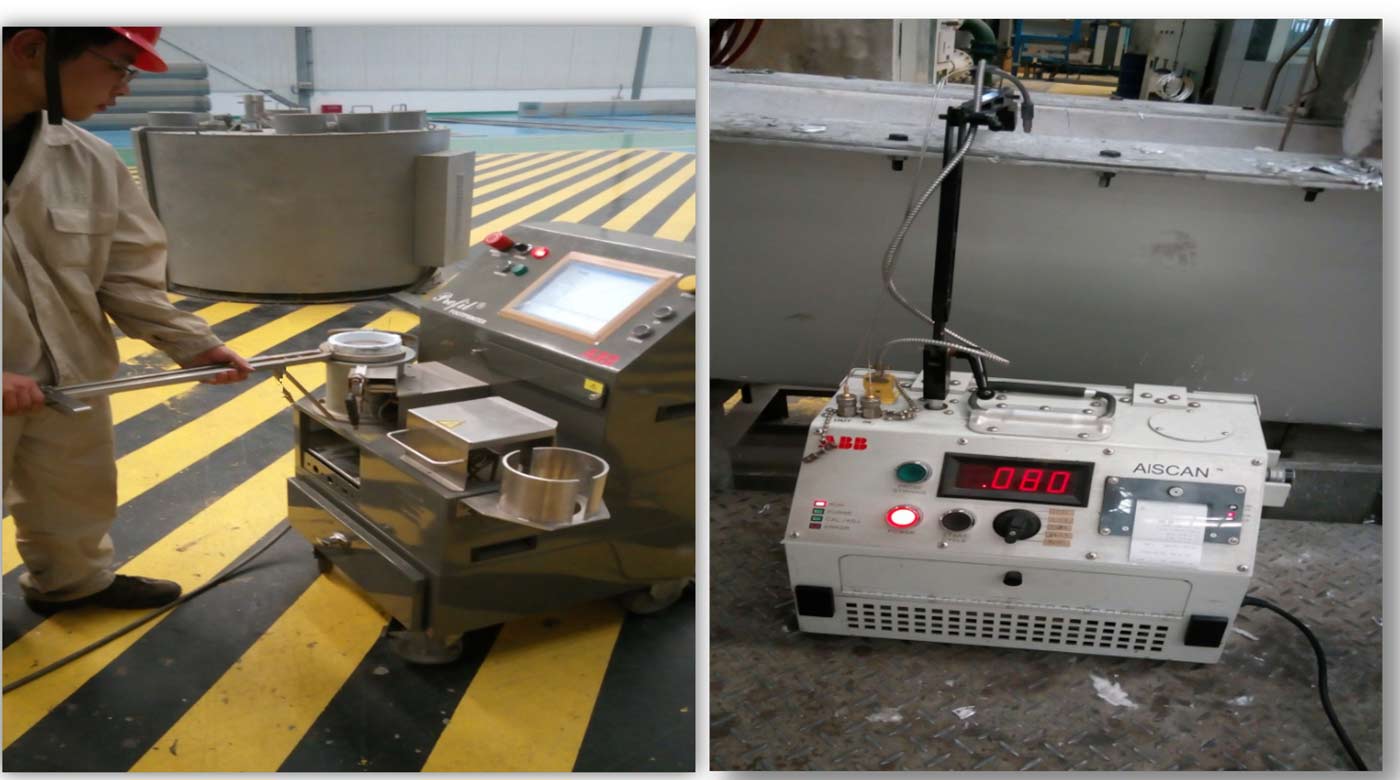
Our company adopts the Alpur three-rotor three-heater online degassing system from Novelis, France, which can vent chlorine and argon at the same time, and its hydrogen removal efficiency is as high as 70% or more. Below 0.12ml/100gAl, the lid and ring pull material can be controlled below 0.14ml/100gAl.
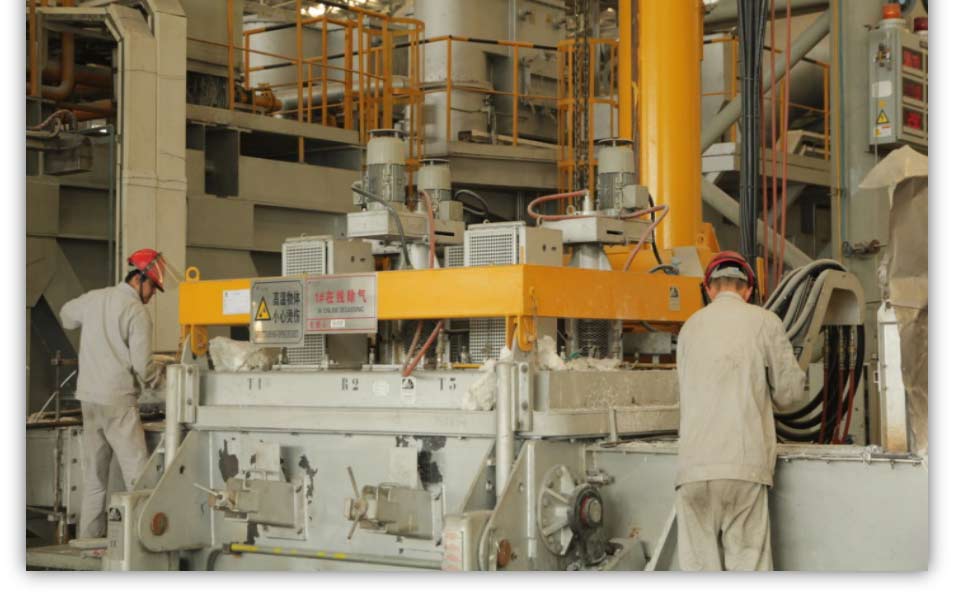
Furnace refining equipment is RFGI graphite rotor rotating jet powder spraying refining equipment designed and produced by Canadian STAS company. It has high refining efficiency and obvious degassing and slag removal. Refining 40-50min can effectively remove most of the hydrogen and hydrogen in the aluminum melt. The slag meets the requirements of high-end products for removing hydrogen and slag, and the hydrogen content of the aluminum outlet is controlled below 0.30 ml/100g-Al.
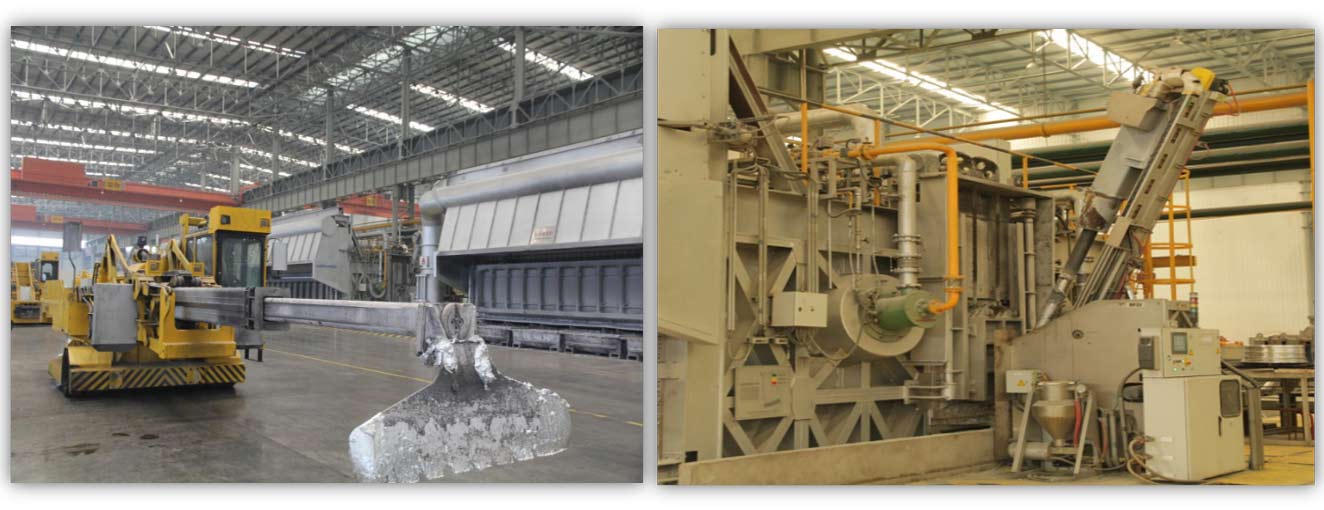
On-line filtration matches the plate filtration and imported tubular filtration of Mitsui Japan. Among them, the plate filter is coarse filtration, and the main function is to extend the service life of the imported filter equipment. The installation of 50PPI filter plate can filter out impurities above 20μm, and the filtration efficiency is 100%; fine filtration (tube filtration) can generally guarantee more than 5μm Most of the impurity particles are filtered out, and the filtration efficiency is above 95%.
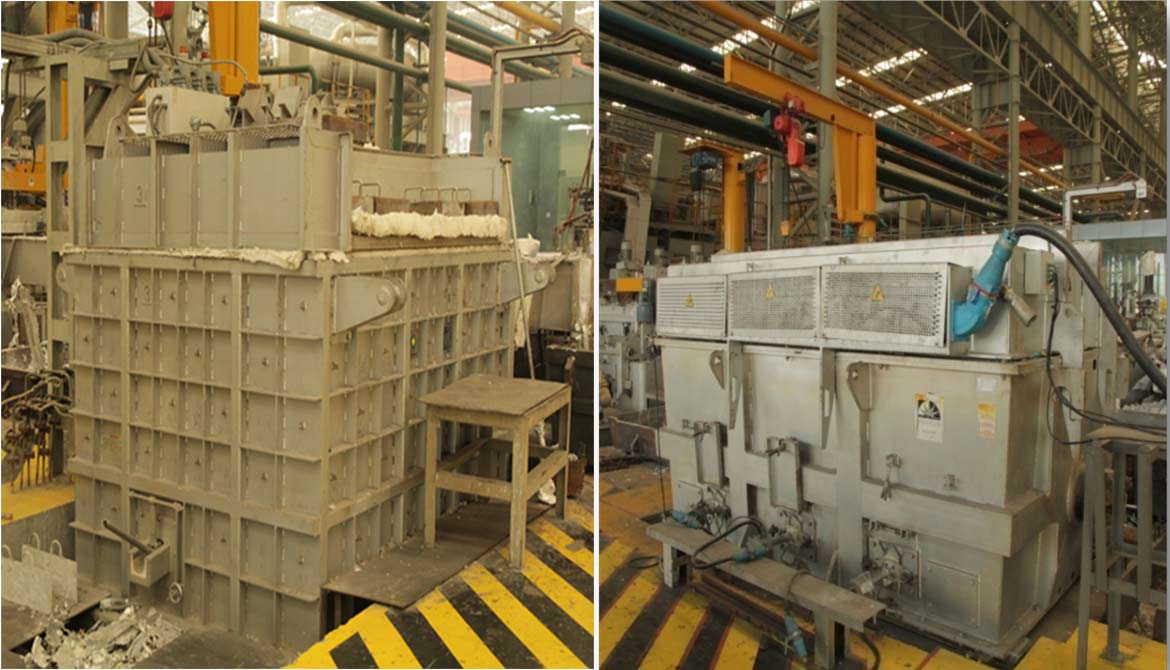
The casting system adopts American Wagstaff casting system, which has strong stability and high safety factor, and adopts LHCTM low-liquid combined slab casting process. The lubricant used only accounts for 3-5% of the consumption of traditional direct condensation casting, and the graphite is The cavity can be replaced, which greatly extends the life of the crystallizer. The slab produced by the LHC process has very slight tail warpage and small shell layer, can obtain high-quality surface and less milling amount, and the yield can reach more than 97%.
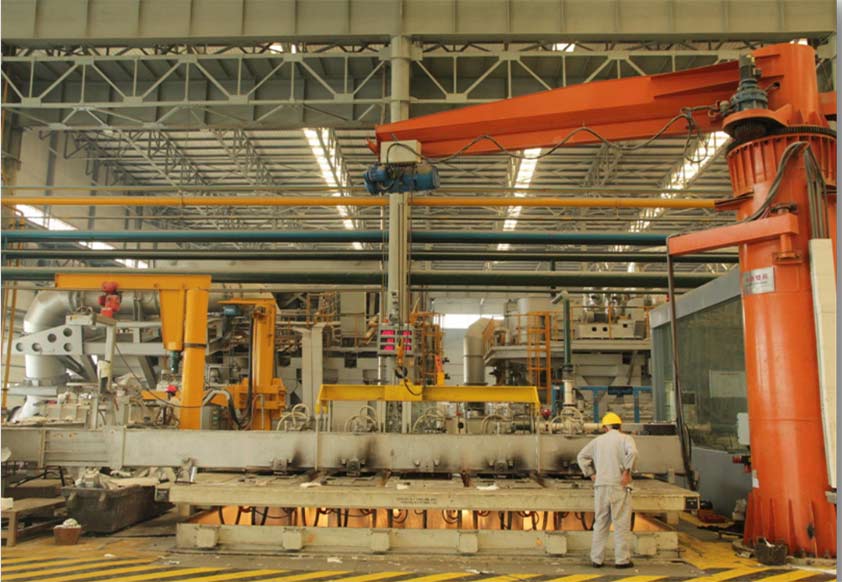
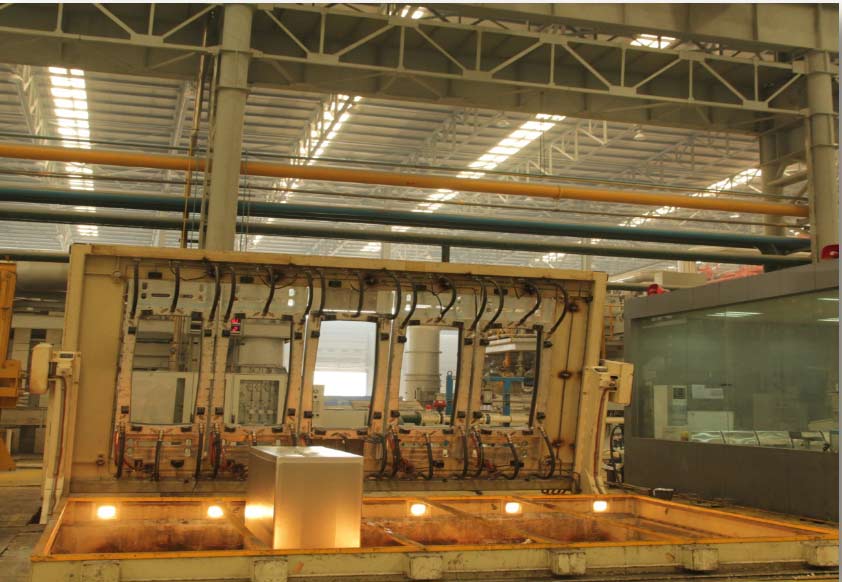
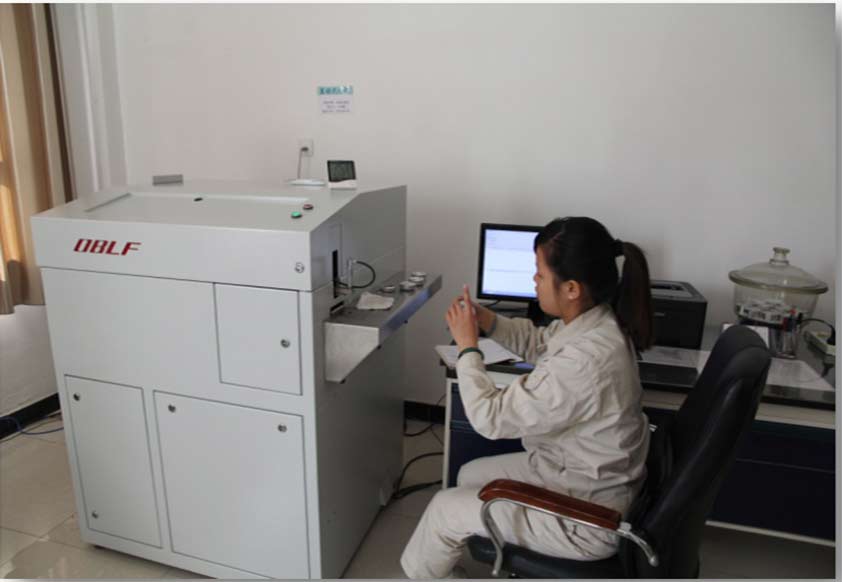
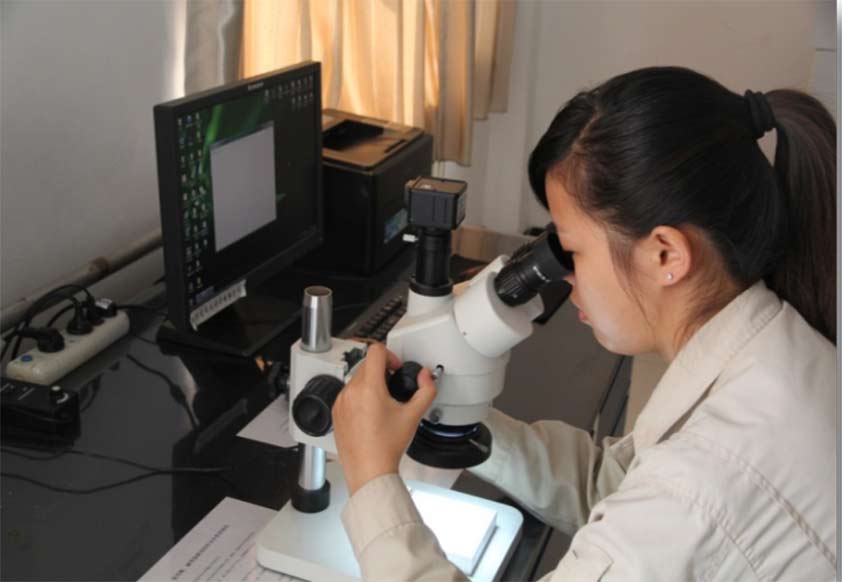
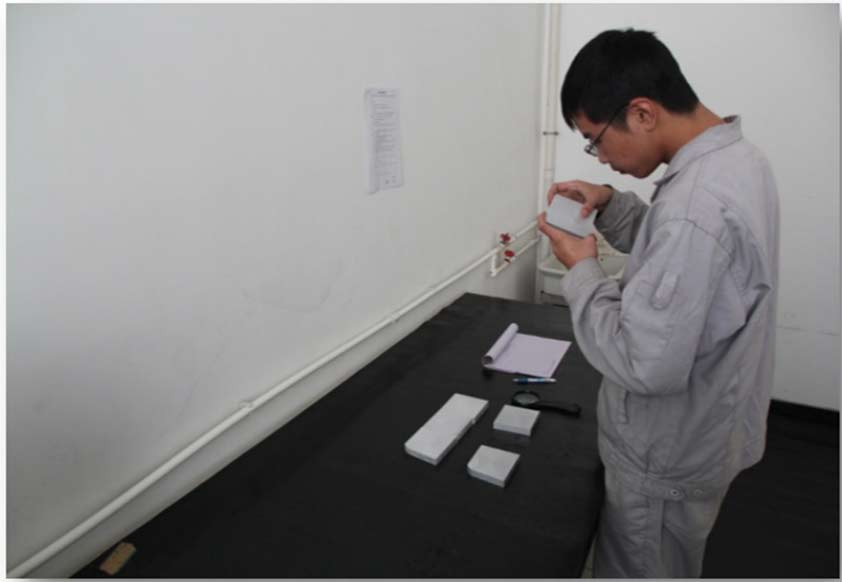
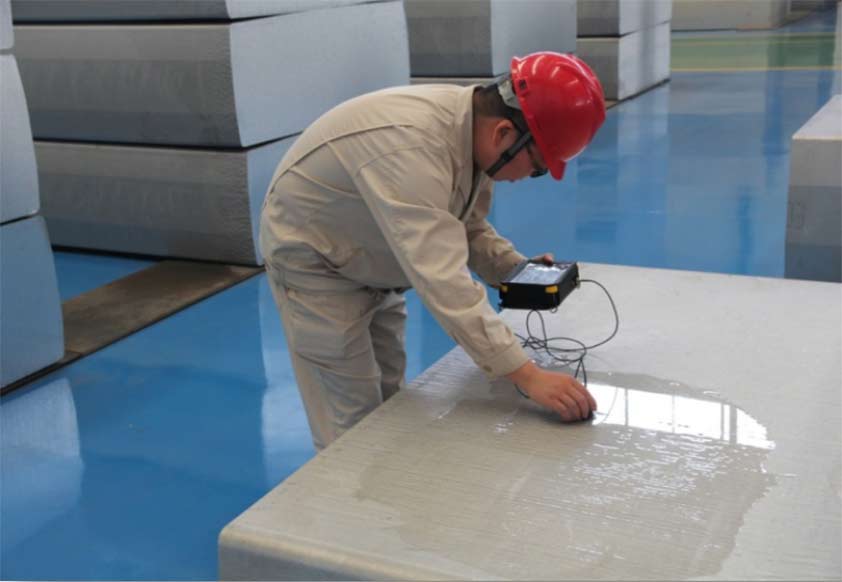
2.Aluminum slab surface quality control
The French Sermas double-head sawing machine can simultaneously cut the head and tail at the maximum speed of 10 blocks per hour. The milling machine is the most advanced model with high precision and high rigidity design from Japan Shingang. The milling machine and the sawing machine are arranged in series. After the slab is sawed, the head and tail are directly conveyed to the #1 milling machine through the roller table for upper and side milling, and then the ingot turning device is automatically turned over and the #2 milling machine completes the other side milling. Greatly improve the efficiency of sawing and milling.
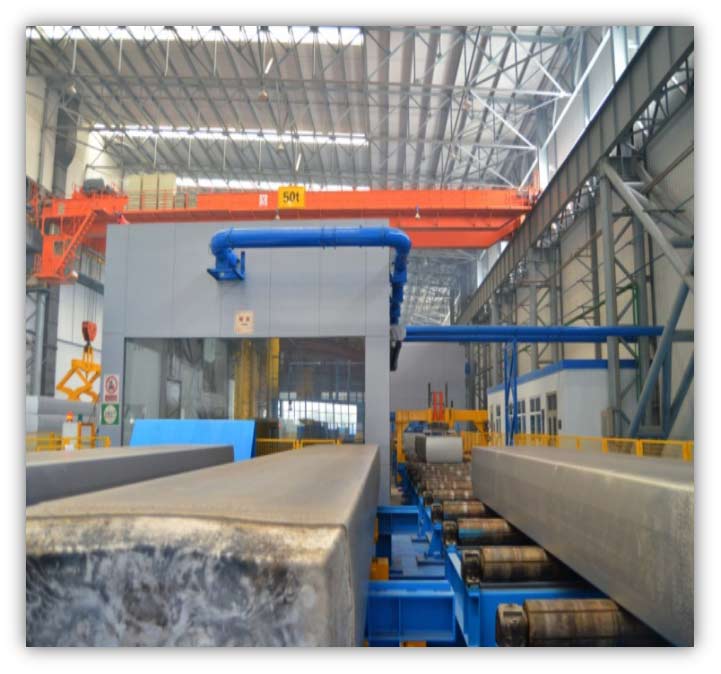
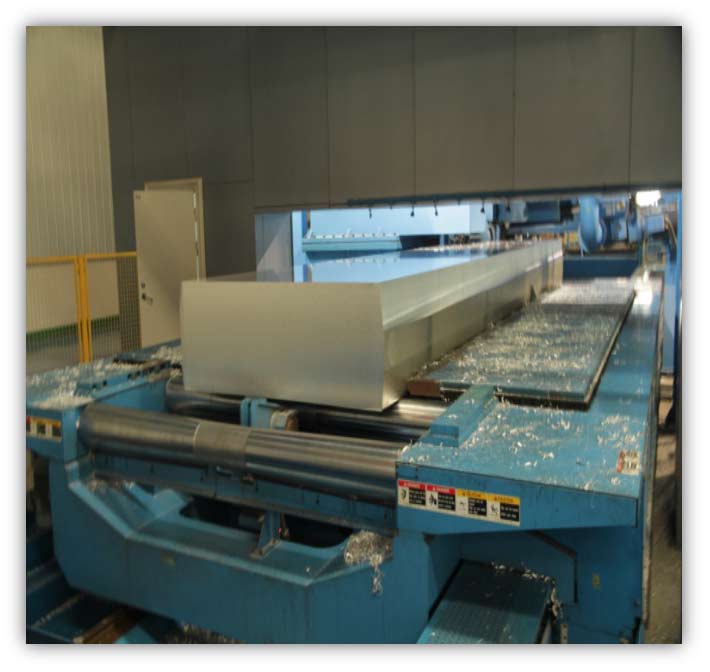
3.Hot rolled plate coil quality control
The hot rolling project adopts the 2560mm hot rolling production line of Germany SMS (1+4). The production capacity of hot-rolled can stock is greater than 760kt/a, the maximum strip width is 2400mm, and the thinnest thickness is 1.8mm. Siemens has advanced electrical configuration, equipped with German IMS convexity meter online, and realizes closed-loop control of thickness and plate shape. The hot strip mill is equipped with hydraulic adjustment system, CVCplus, work roll bending and multi-zone cooling system, temperature control system, equipped with light shears, heavy shears, edge trimmers, coilers, waste transportation systems, flue gas purification systems, etc.
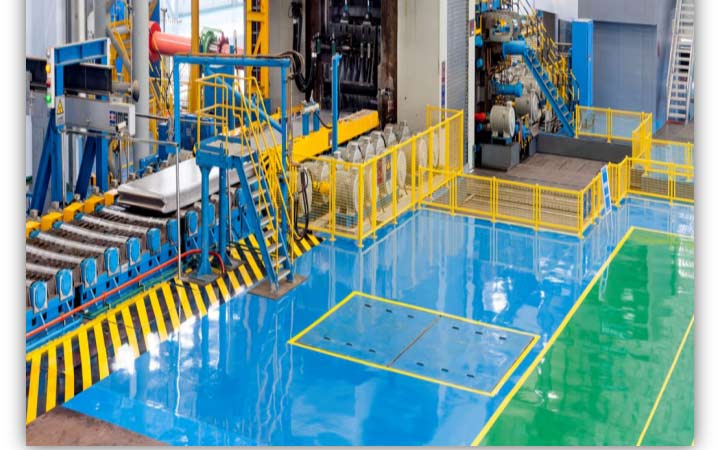
Four slab heating vertical push furnaces are designed by Otto Junker and manufactured by Suzhou Xinchangguang. The maximum thickness of the ingot is 620mm. Each furnace has a maximum furnace capacity of 860 tons, and can hold 25 34t slabs. All four furnaces have heating and soaking functions, which can meet the needs of heating and soaking different product processes.
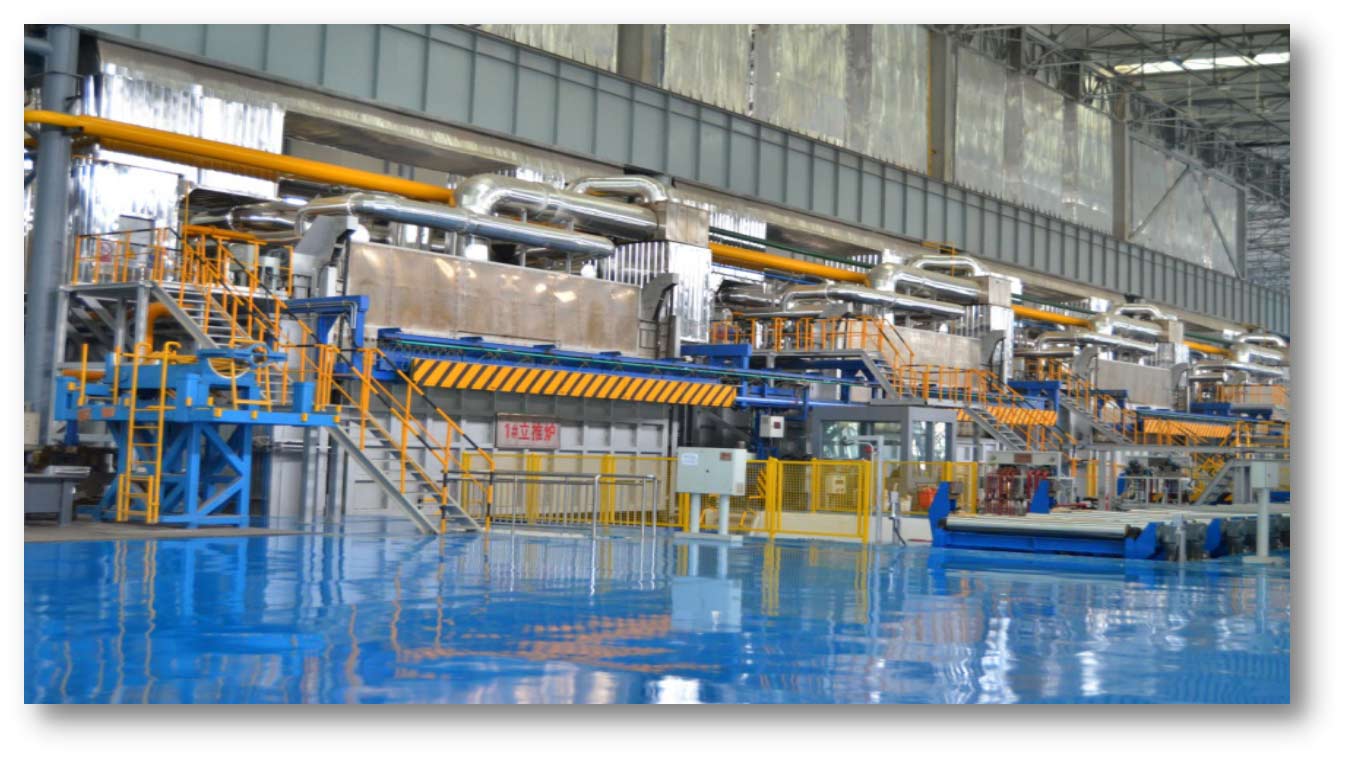
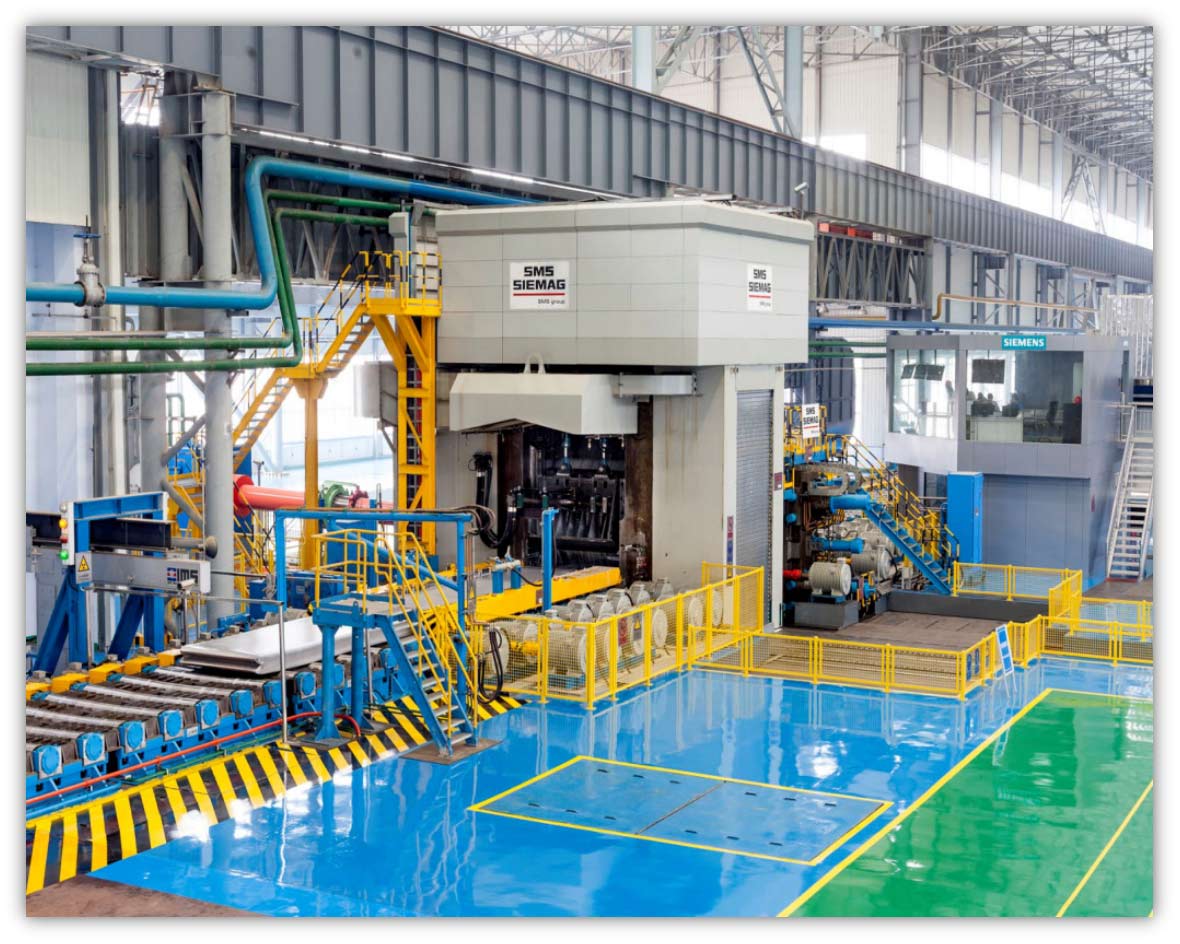
Rough rolling mill
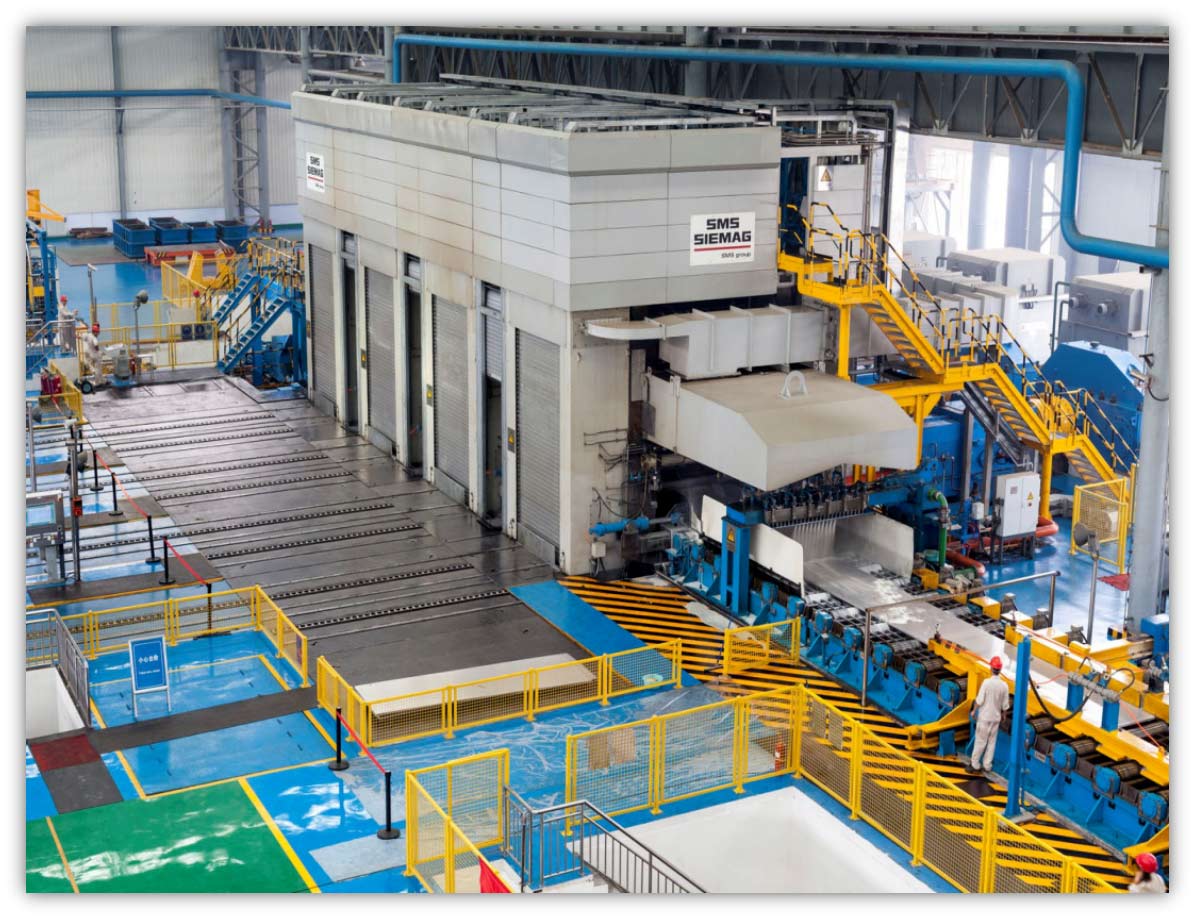
Finishing mill
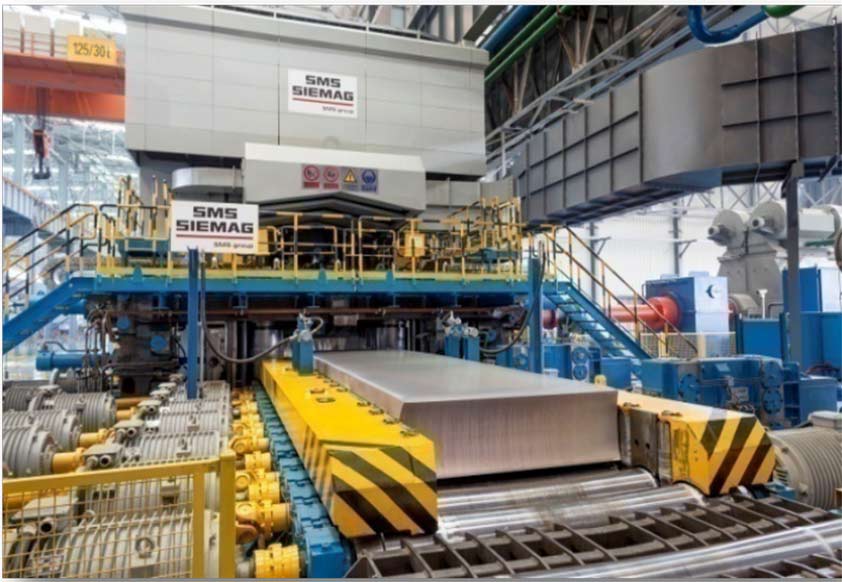
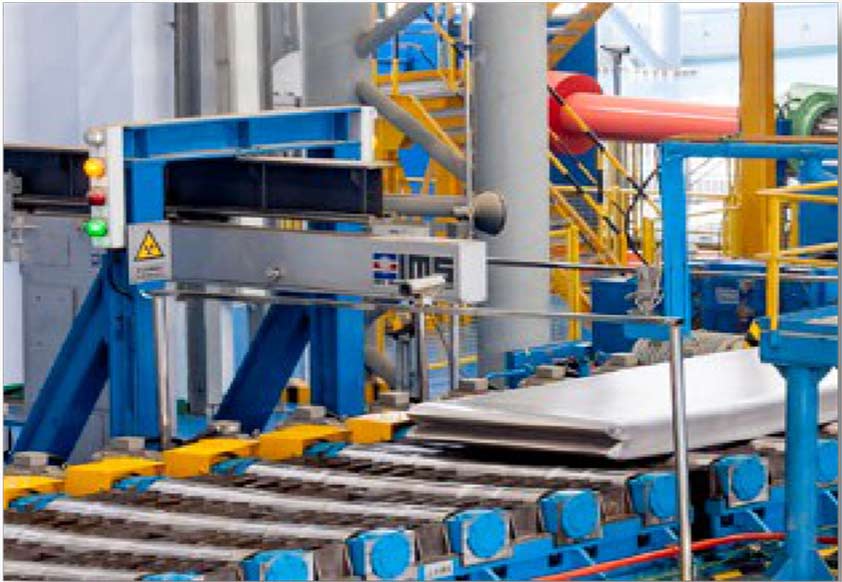
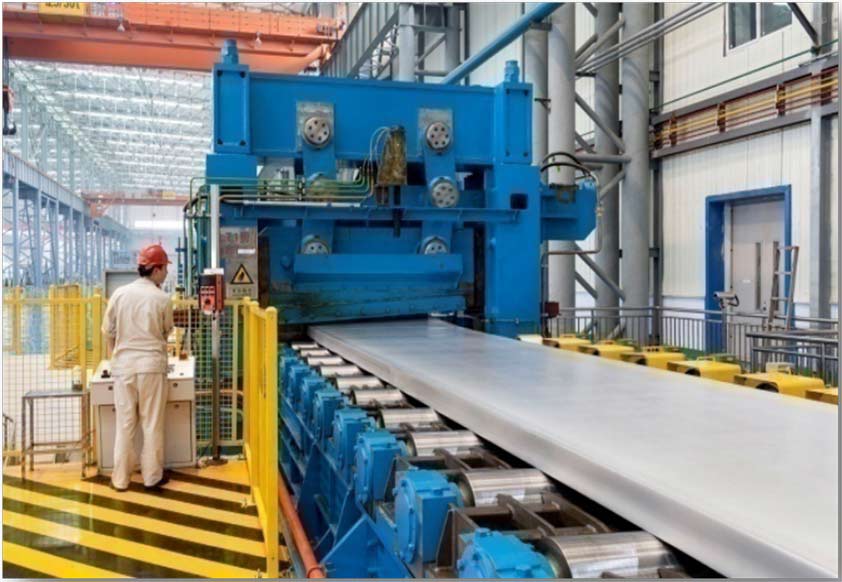
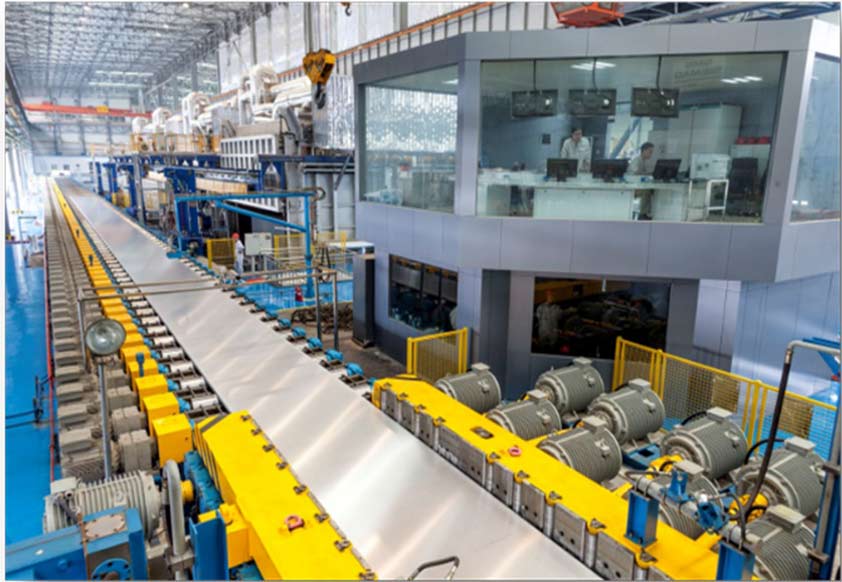
The work roll CVCplus achieves ±100mm shifting amount, which can meet the customer's convexity requirements of various alloys. The control range is 0.2-1.0%, which truly realizes the requirements of controllable convexity. The SMS design of the finishing mill has the fastest rolling speed, and the F4 export reaches V=600mpm (that is, 600m/min).
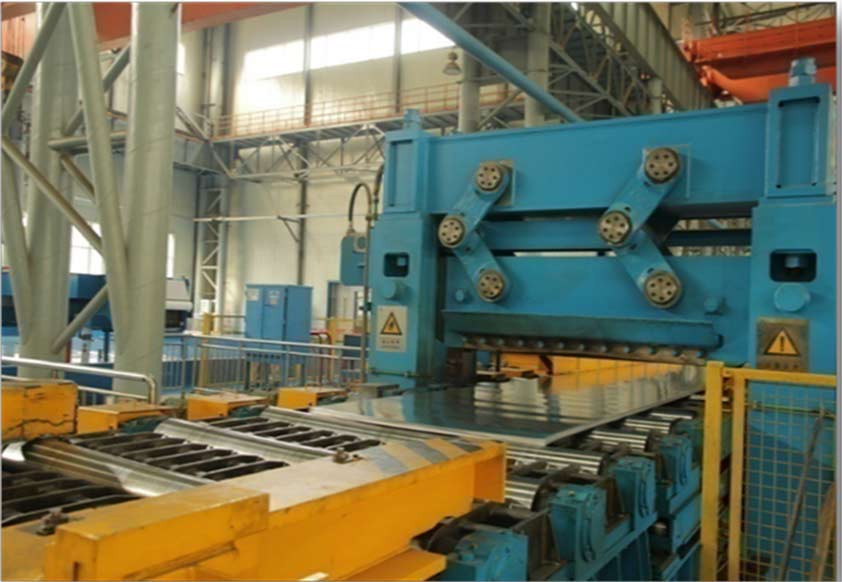
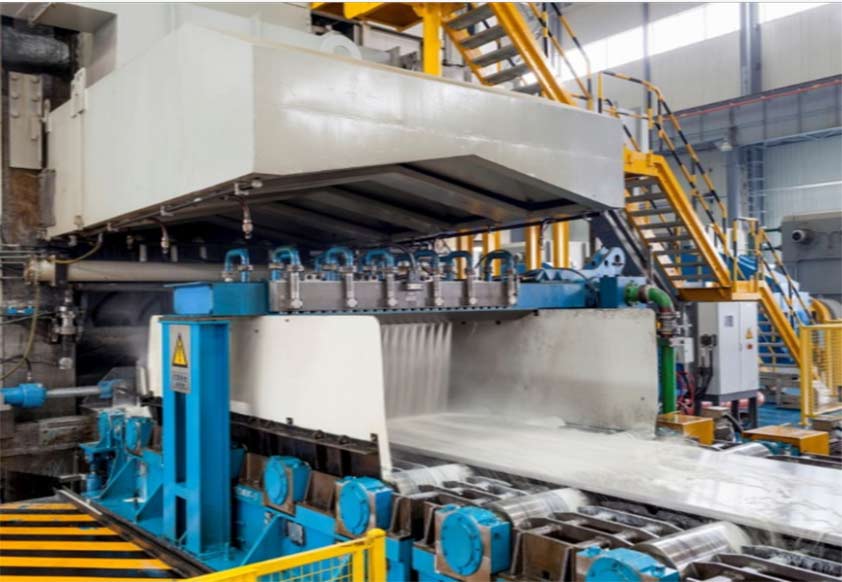
Finished rolling export surface quality detector, equipped with advanced Cognex surface quality inspection, can simultaneously inspect the upper and lower surface defects of strips online, with an inspection accuracy of 98%.
The final rolling thermometer at the finish rolling outlet and the final rolling thermometer at the finish rolling outlet measure ±4℃, which can accurately control the final rolling temperature of the product.
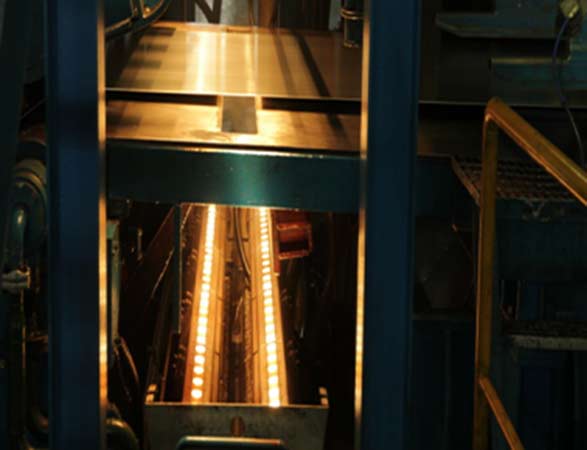
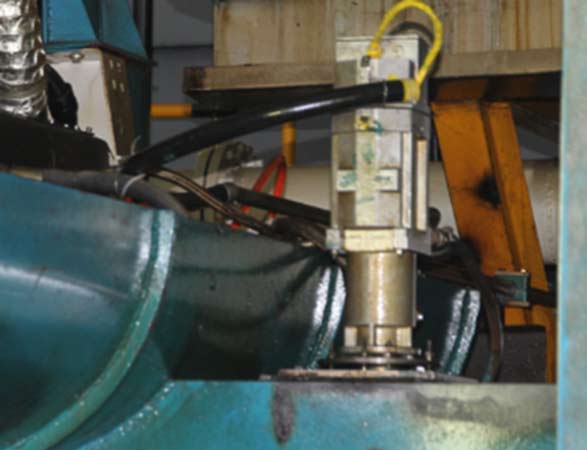
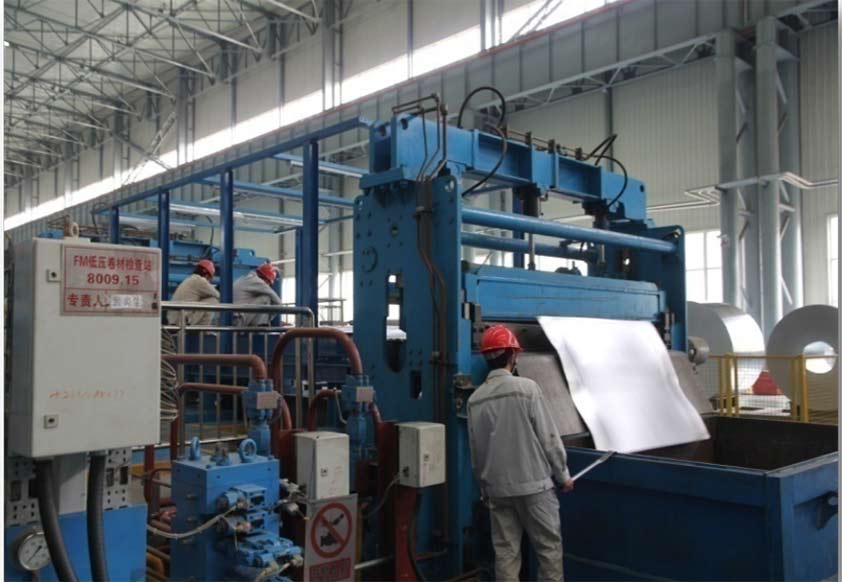
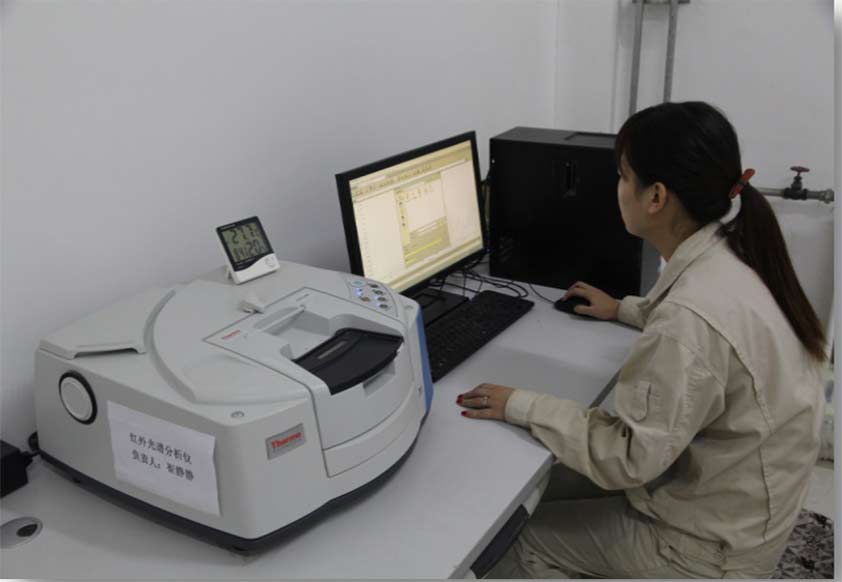
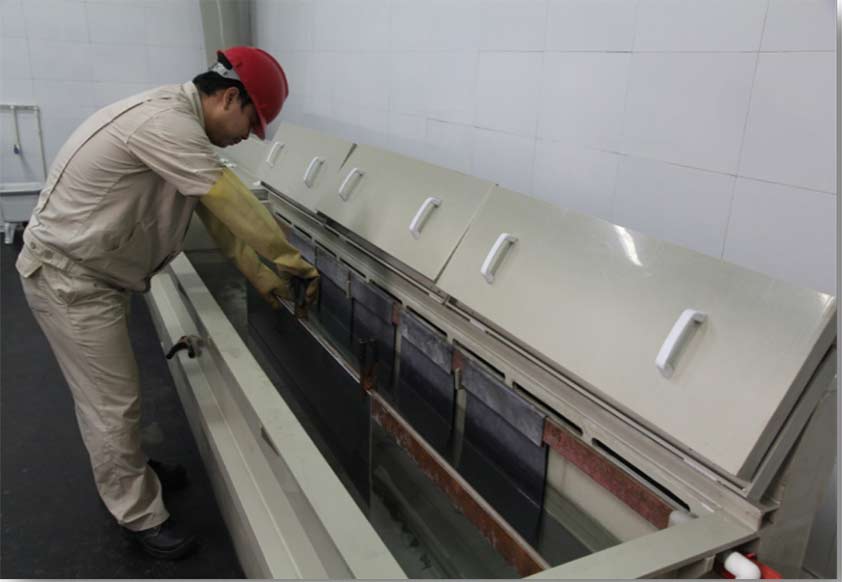
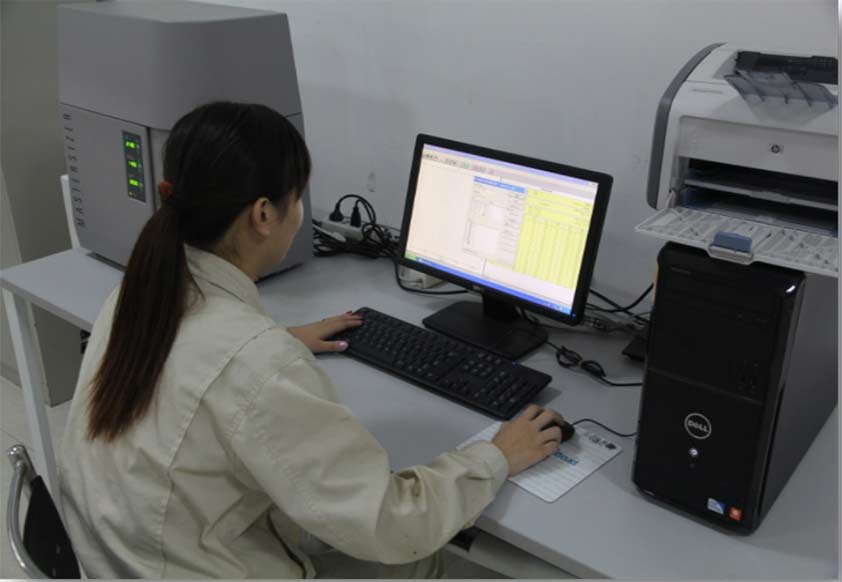
4.Roller quality control
The German Hercules grinding machine adopts fully automatic grinding technology, has adaptive control capability, and is equipped with a special system for advanced roll shape generation. It can realize automatic online measurement and inspection of rolls under high requirements and continuous operation conditions. The fully automatic CNC control in the grinder configuration can detect and automatically repair the roll shape online, with a control accuracy of 0.00001mm.
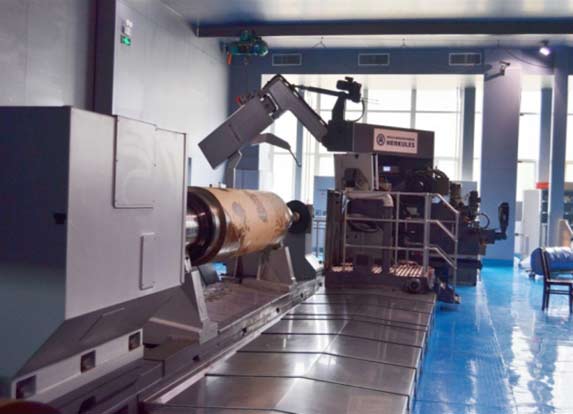
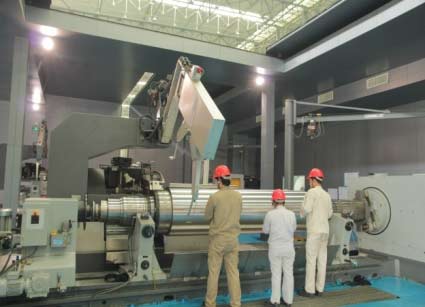
5.Cold rolled product quality control
The cold rolling project adopts German SMS 2500mm single stand CVC cold rolling mill and 2500mm double stand CVC cold rolling mill, strip width maximum 2400mm, minimum 900mm, coil size: coil outer diameter maximum 2750mm, minimum 1200mm. The maximum rolling force is 20000kN, the maximum rolling speed: 1800m/min. And matching German Danieli 2300mm edge trimming machine and slitting machine, German Engle Straightening machine, German Herkules grinder, South Korea Pohang Iron & Steel packaging line and German Vollert high-bay warehouse.
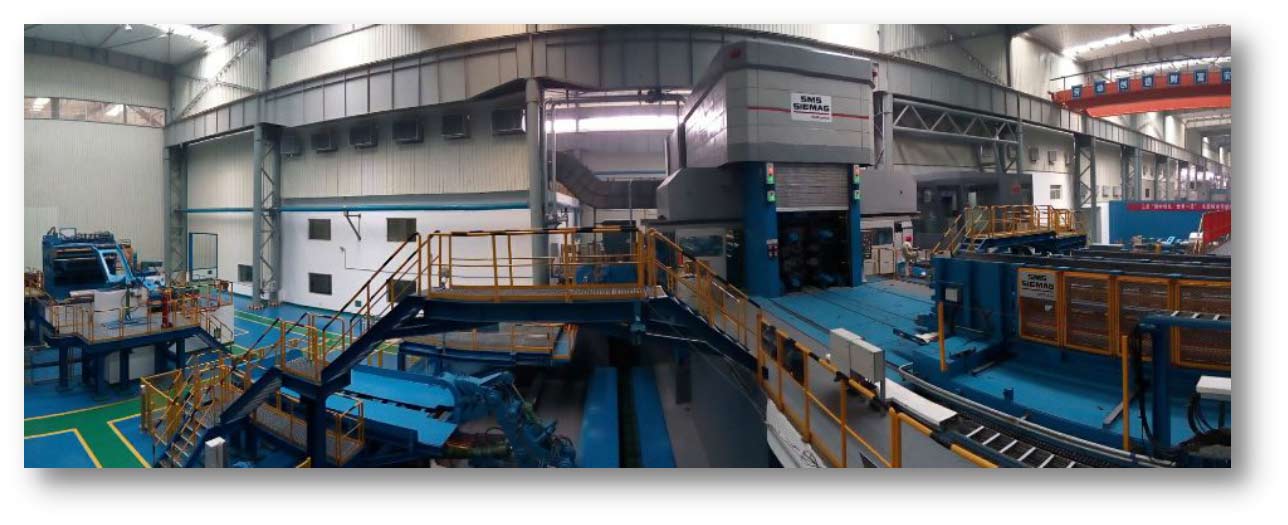
6.Technology support world widely
(1) Hire an international technical team: South African Aluminum , Houghton Corporation Emulsion , Alcan and Australian Aluminum Corporation And the former chief engineer of Alcan, and other foreign expert groups regularly provide monthly technical guidance;
(2) Hire domestic technical teams: Alcoa, Nanshan Aluminum, Asia Aluminum High-end aluminum deep processing technical personnel to our company in charge of process, technology, quality and other work.
